Pressure Die Casting Manufacturers: Revolutionizing Metal Fabrication
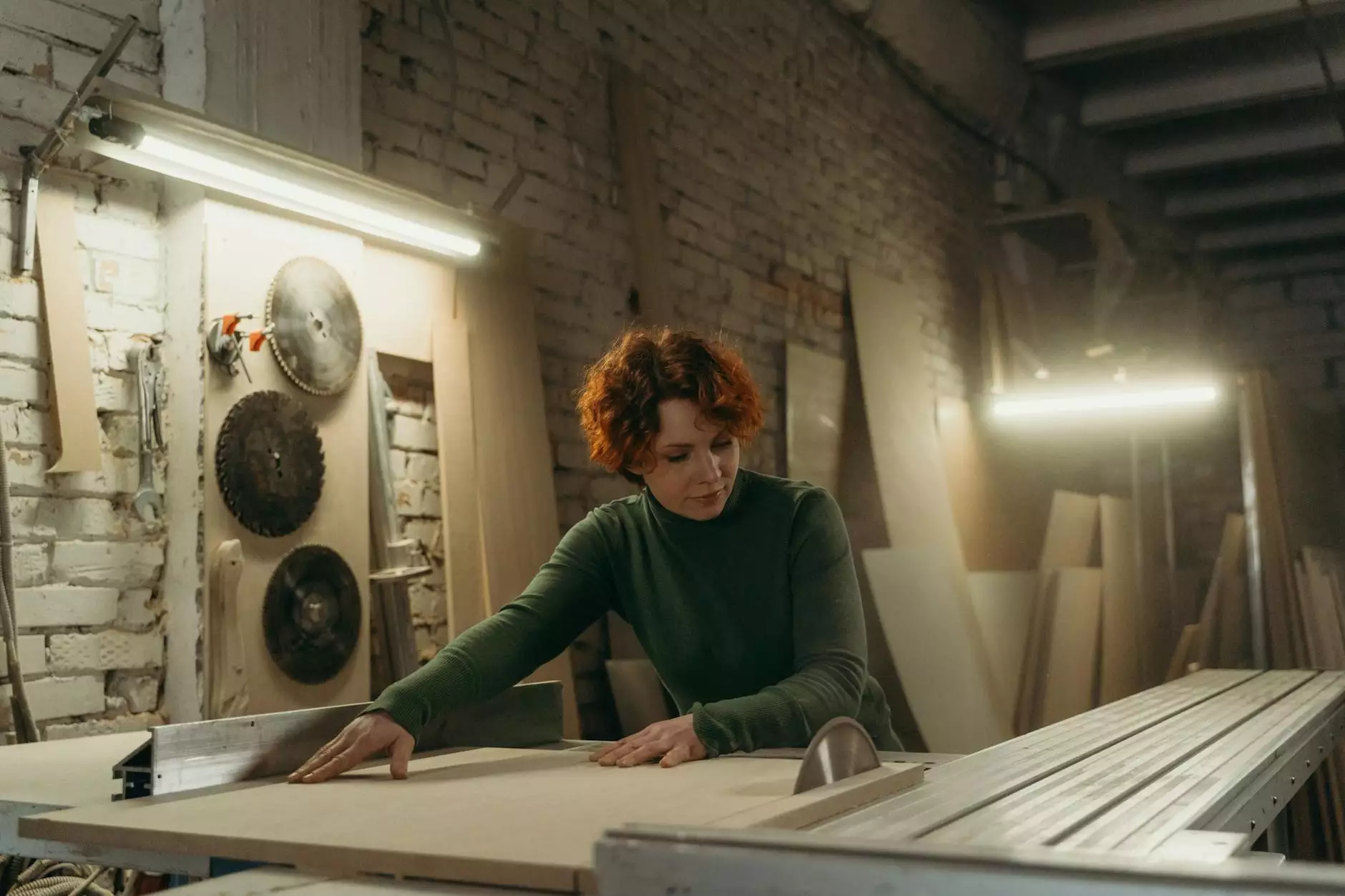
The landscape of industrial manufacturing has evolved significantly over the years, and among the many innovative techniques, pressure die casting has emerged as a revolutionary method that offers remarkable advantages for metal fabricators. This article delves deep into the realm of pressure die casting manufacturers, examining their pivotal role in the industry, the benefits they provide, and the applications of their products.
Understanding Pressure Die Casting
Pressure die casting is a manufacturing process that involves forcing molten metal into a mold cavity under high pressure. This technique is predominantly used for metals like aluminum, zinc, and magnesium. Unlike other casting methods, pressure die casting allows for the production of complex shapes with high dimensional accuracy and smooth surface finishes.
The Evolution of Die Casting Techniques
The development of die casting can be traced back to the early 19th century. Over time, manufacturers have fine-tuned the process, introducing advanced technologies and automation. Today, pressure die casting stands out due to its effectiveness in mass production, leading to increased efficiency and reduced costs.
The Key Advantages of Pressure Die Casting
- High Production Efficiency: Pressure die casting manufacturers can produce a large number of parts in a short period, making it ideal for high-volume production runs.
- Dimensional Accuracy: The process ensures that the parts produced are incredibly precise, which is crucial for industries that require tight tolerances.
- Excellent Surface Finish: The resulting cast parts feature smooth finishes that often require little to no extra processing.
- Material Utilization: The pressure application reduces scrap rates, allowing more efficient use of materials.
- Complex Shapes: The technique allows for intricate designs, enabling manufacturers to innovate without compromising quality.
Applications of Pressure Die Cast Components
Pressure die casting is widely used across various industries. Here are some of the main sectors benefiting from this technology:
Automotive Industry
The automotive sector utilizes pressure die casting extensively to manufacture critical components such as engine blocks, transmission housings, and wheel rims. The strength-to-weight ratio provided by die-cast aluminum parts is a crucial factor in enhancing fuel efficiency and vehicle performance.
Consumer Electronics
In the realm of consumer electronics, pressure die casting manufacturers produce parts for mobile devices, laptops, and home appliances. The precision and aesthetics of die-cast components are vital, meeting the design sophistication required by modern electronics.
Aerospace Sector
The aerospace industry demands components that must withstand extreme conditions while maintaining lightweight characteristics. Pressure die casting enables manufacturers to create robust parts that adhere to stringent safety regulations.
Industrial Equipment
Various industrial applications utilize die casting for making high-load components like gearboxes and housings. The durability and reliability of these components are critical for machinery that operates under harsh conditions.
Choosing the Right Pressure Die Casting Manufacturer
As the demand for die-cast products increases, so does the number of pressure die casting manufacturers. Selecting the right one is essential for ensuring quality and efficiency. Here are some key considerations when choosing a manufacturer:
Expertise and Experience
Look for manufacturers with a proven track record in the pressure die casting sector. Experience often correlates with expertise in handling complex projects and adhering to industry standards.
Quality Assurance
High-quality output should be non-negotiable. Manufacturers should have rigorous quality control processes to guarantee that all products meet the required specifications.
Technological Capability
Modern pressure die casting requires advanced machinery and technology. Ensure that the manufacturer utilizes state-of-the-art equipment capable of producing high-quality results.
Material Selection
The choice of materials significantly impacts the performance of the final product. A good manufacturer should offer a variety of material options, tailoring solutions to specific application needs.
Customer Support and Collaboration
Collaboration is vital in any manufacturing process. Choose a manufacturer that values communication and is willing to work closely with you to achieve your goals.
The Future of Pressure Die Casting Manufacturing
The future of pressure die casting manufacturing appears bright as industries are increasingly recognizing the benefits of using this method. Innovations in technology, materials, and processes will continue to shape the landscape, offering even more opportunities for efficiency and sustainability.
Sustainable Practices
With a growing emphasis on sustainability, pressure die casting manufacturers are adopting greener practices. This includes optimizing processes to minimize energy consumption and waste while maximizing the recycling of materials.
Advanced Automation
The integration of automation and smart technologies will further enhance precision and efficiency in pressure die casting. Manufacturers who embrace Industry 4.0 technologies will be well-positioned to lead in the competitive landscape.
Conclusion
In conclusion, pressure die casting manufacturers play a vital role in the metal fabrication industry, offering innovative solutions that meet the diverse needs of modern manufacturing. With their ability to produce high-quality, precise components efficiently, these manufacturers are not only enhancing productivity but also driving the future of industrial manufacturing.
As the industry evolves, companies like DeepMould.net stand at the forefront, providing unparalleled services to clients across various sectors. By understanding the advantages and applications of pressure die casting, businesses can leverage this technology to advance their operations and enhance their product offerings.